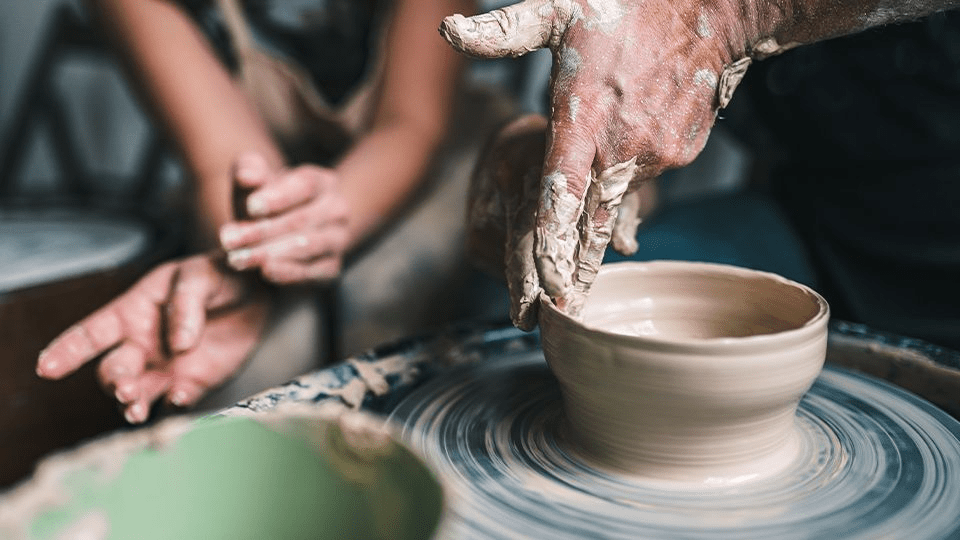
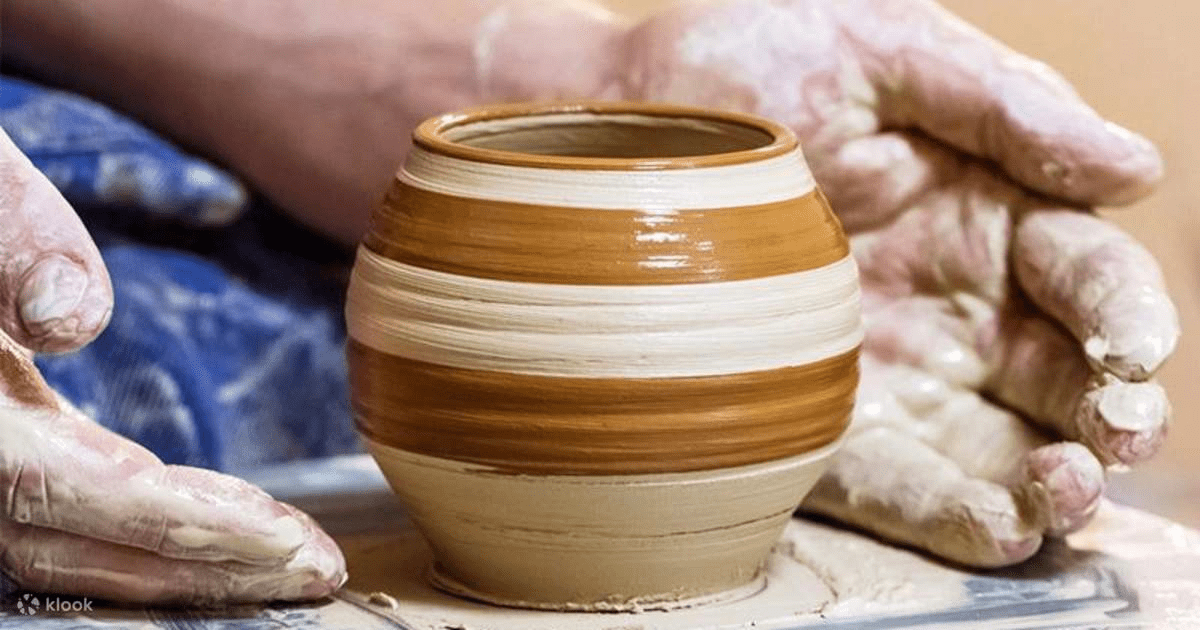
Products used in ceramics are mainly CMC
The use of CMC in the ceramic body can increase the plasticity of the sand material, facilitate the molding of the body, and increase the flexural strength of the green body. It is a good reinforcing agent; the use of CMC in glaze slurry and flower glaze can be used as a binder. The functions of suspension, decoagulation and water retention.
Sodium carboxymethyl cellulose CMC for ceramics
Application in ceramic body
Sodium carboxymethylcellulose CMC for ceramics has a unique linear polymer structure. When CMC is added to water, its hydrophilic group combines with water to form a solvation layer, which gradually disperses CMC molecules in the water. CMC polymers rely on hydrogen Bonds and van der Waals forces form a network structure, thereby exhibiting adhesion. CMC for ceramic embryos can be used as an excipient, plasticizer, enhancer, etc. for embryos in the ceramic industry:
1. The dosage is small, and the flexural strength of the green body is significantly increased;
2. Increase green processing speed and reduce production energy consumption;
3. It has good ignition loss property, no residue after burning, and does not affect the color of the blank;
4. Facilitates process operation and prevents defects such as glaze rolling and lack of glaze;
5. It has a decoagulation effect, which can improve the fluidity of glaze slurry and facilitate glaze spraying operations;
6. As an excipient for the blank, it increases the plasticity of the clay and sand materials and facilitates the molding of the blank;
7. Strong resistance to mechanical wear and less molecular chain damage during ball milling and mechanical stirring;
8. As a blank reinforcing agent, it can increase the flexural strength of the green blank, improve the stability of the blank, and reduce the breakage rate;
9. Strong suspension and dispersion, which can prevent the agglomeration of infertile raw materials and color slurry particles and make the slurry disperse evenly;
10. Evaporate the moisture in the blank evenly to prevent drying and cracking. It is especially used for large-size floor tile blanks and polished tile blanks, and the effect is obvious.
Sodium carboxymethyl cellulose CMC for ceramics
Application in ceramic glaze slurry
Sodium carboxymethylcellulose CMC for ceramics belongs to the polyelectrolyte category. It mainly acts as a binder in the glaze slurry and also plays a suspending role. When CMC is added to the glaze slurry, water penetrates into the inside of the CMC glue block, and the hydrophilic group combines with water, causing water absorption and expansion. At the same time, the inside of the micelle is hydrating and expanding, and a bound water layer is formed outside. The micelle is free from the glue in the initial dissolution stage. In the liquid, due to the asymmetry in size and shape, and the regular interference with each other through van der Waals forces, the combined water layer gradually forms a network structure with a large volume, so it has strong adhesion ability:
1. Under low dosage conditions, it can effectively adjust the rheology of glaze slurry and facilitate glaze application;
2. Improve the bonding properties of the base and glaze, significantly increase the strength of the glaze and prevent deglazing;
3. The glaze has high fineness and stable glaze slurry, and can reduce glaze pinholes after sintering;
4. Excellent dispersion and protective colloid properties, which can keep the glaze slurry in a stable dispersion state;
5. Effectively increase the surface tension of the glaze, prevent water from diffusing from the glaze into the body, and increase the smoothness of the glaze surface;
6. Avoid cracking and printing breakage during transportation due to the decrease in strength of the green body after glazing.
Sodium carboxymethyl cellulose CMC for ceramics
Application in ceramic printing glaze
Sodium carboxymethyl cellulose CMC for ceramics has good solubility, high solution transparency, and almost no insoluble matter. It has excellent shear dilution and lubricity, which can greatly improve the printing adaptability and post-processing effect of the printing glaze. At the same time, CMC has good thickening, dispersing and stabilizing effects when used in ceramic printing glazes:
1. Good printing rheology ensures smooth printing;
2. The printed pattern is clear and the color is consistent;
3. The solution has high fineness, good lubricity and good use effect;
4. It has good water solubility, almost no insoluble matter, does not stick to the net, and does not block the net;
5. The solution has high transparency and good network penetration;
6. Excellent shear thinning properties, greatly improving the printing adaptability of the printing glaze;
Sodium carboxymethyl cellulose CMC for ceramics
Application in ceramic infiltration glaze
The infiltration glaze contains a large amount of soluble salt substances and is somewhat acidic. The Lude Chem ceramic sodium carboxymethyl cellulose CMC used for the infiltration glaze has excellent acid and salt resistance, allowing the infiltration glaze to maintain a stable viscosity during use and placement. , to prevent color difference due to changes in viscosity, and greatly improve the stability of the bleeding glaze:
1. Good solubility, no clogging, and good mesh penetration;
2. It has good matching with the glaze to make the glaze stable;
3. Good acid and alkali resistance and salt resistance, which can keep the viscosity of the seepage glaze stable;
4. The solution has good leveling performance and good viscosity stability, which can prevent color difference caused by changes in viscosity.